Kaizen encourages you to make small, incremental improvements consistently across your processes, fostering a mindset of continuous growth. By focusing on tiny, manageable changes, you can boost efficiency, quality, and engagement without overwhelming your team. Involving everyone and tracking results helps sustain momentum. When you keep refining step-by-step, improvement becomes a natural part of your culture. If you continue exploring, you’ll discover how to turn these small steps into lasting success.
Key Takeaways
- Kaizen promotes ongoing, incremental improvements rather than seeking perfection all at once.
- Small, consistent changes build momentum, leading to significant long-term gains.
- It encourages employee involvement to identify problems and suggest practical solutions.
- Regularly questioning and analyzing workflows helps uncover smarter ways of working.
- Standardizing successful small improvements ensures they become part of everyday routines.
Understanding the Core Philosophy of Kaizen

Understanding the core philosophy of Kaizen means recognizing that continuous improvement is a mindset, not a one-time effort. You see, Kaizen emphasizes ongoing, incremental changes across all areas of work and life. It rejects the idea of perfection, focusing instead on gradual enhancement over time. Small, consistent improvements build up, creating a cumulative effect that boosts efficiency, quality, and adaptability. Everyone in the organization shares responsibility for these improvements, fostering a culture of collective effort. You’re encouraged to question existing processes regularly, seeking smarter ways to work. This mindset promotes innovation and flexibility, helping you stay competitive and responsive. Embracing Kaizen means adopting a mindset that values progress, no matter how small, as a powerful driver of long-term success. Additionally, understanding projector technology can help you identify areas for incremental improvement in your home cinema setup, and applying principles from economic theories and principles can optimize resource allocation in your personal projects. Cultivating curiosity about continuous improvement strategies can further enhance your ability to implement Kaizen effectively. Recognizing that company culture plays a vital role in sustaining these improvements can motivate teams to embrace change more readily.
The Implementation Cycle of Continuous Improvement
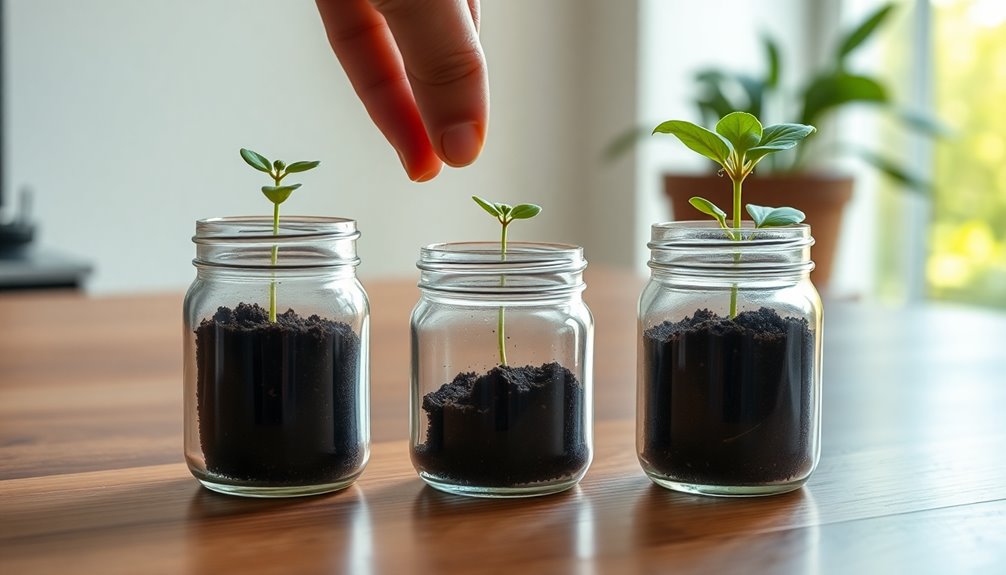
The implementation cycle of continuous improvement is a systematic process that transforms identified issues into lasting enhancements. You start by recognizing problems or opportunities through thorough observation and data collection. Engaging employees across all levels encourages proactive problem spotting and idea generation. Next, you analyze workflows using tools like process mapping to uncover root causes, ensuring solutions target fundamental issues. Brainstormed solutions are then tested on a small scale, with performance measured to evaluate effectiveness. Based on results, you make adjustments before deploying successful solutions organization-wide. Standardizing these improvements embeds changes into daily routines, supported by documentation and clear communication. Incorporating natural materials such as wood and linen can also enhance the authenticity of the improvements. Additionally, fostering a problem-solving mindset among team members promotes ongoing innovation and adaptation. The cycle then repeats, with each iteration building on previous lessons, fostering a culture of continuous, incremental progress driven by collective effort and management support. Moreover, understanding the importance of drivetrain maintenance can help prevent operational issues and sustain improvements over time. Recognizing the value of visual and auditory cues can further aid in reinforcing new processes and ensuring consistent implementation. Incorporating diverse approaches such as different techniques and perspectives can also enrich the problem-solving process.
Roots of Lean Manufacturing and Waste Reduction
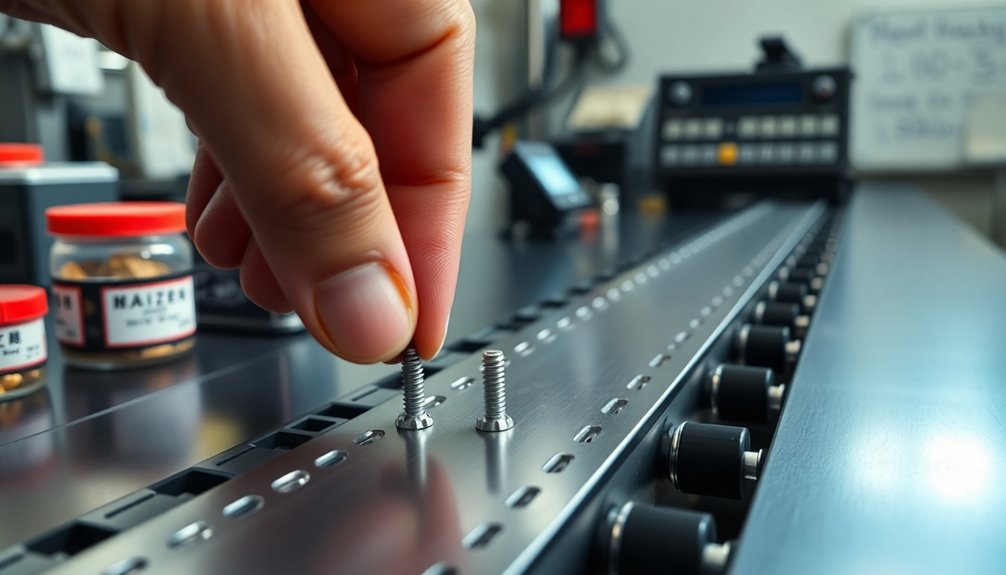
The origins of lean manufacturing and waste reduction trace back to early 20th-century innovations in mass production. You can see this in Henry Ford’s flow production, which introduced standardized parts and minimized operator movements while aligning supply chains with demand through just-in-time principles. However, mass production had limitations, such as focusing on a single model and lacking flexibility, which led to waste. Ford’s innovations laid the groundwork by eliminating non-value-added activities and enabling consistent quality through interchangeable parts. Later, Toyota’s contributions expanded these ideas with self-stopping looms, human-centered design, and resource-efficient, demand-driven production. These foundational concepts evolved into structured waste reduction frameworks, formalizing the identification and elimination of muda, setting the stage for continuous improvement practices we still use today. The importance of inspirational leadership and fostering a culture of ongoing improvement further strengthened lean methodologies over time. Additionally, the development of standardized work techniques has been crucial in maintaining process consistency and reducing variability, thus further minimizing waste. Moreover, a comprehensive understanding of the refrigeration cycle has enabled manufacturers to optimize energy use and further reduce waste in production environments.
Engaging Employees in Small-Scale Changes
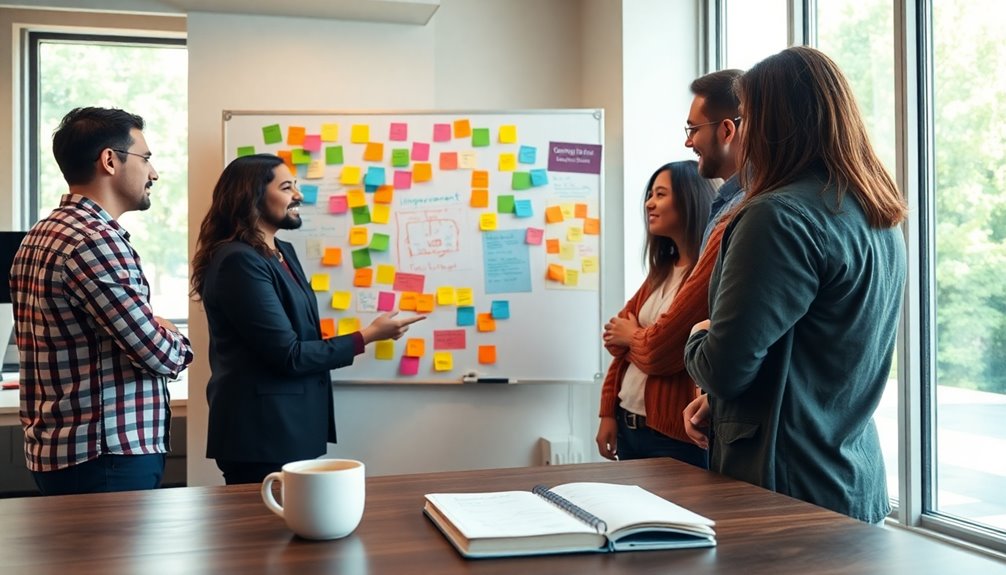
Engaging employees in small-scale changes is essential for fostering a culture of continuous improvement. When you involve team members in the process, it reduces resistance by easing the *shift* and making changes feel manageable. Giving employees a voice in decision-making boosts their commitment and ownership of improvements. Encouraging them to propose ideas creates a sense of empowerment and drives innovation. Clear communication and ongoing feedback keep everyone aligned and motivated. Breaking down large changes into smaller steps minimizes uncertainty and stress, helping staff adapt more smoothly. When employees see their suggestions implemented, their satisfaction and creativity grow. This active involvement not only accelerates improvements but also builds trust, making continuous change a natural part of your organization’s culture. Understanding the legal process of divorce can also help individuals navigate personal transitions more smoothly during times of change. Incorporating employee engagement strategies informed by best practices can further enhance participation and success in these initiatives. Additionally, providing proper training and support ensures employees feel confident and capable of sustaining improvements over time. Moreover, recognizing and addressing psychological responses such as fears or anxieties can help maintain a positive environment for ongoing development. To further facilitate these efforts, integrating wellness programs that promote mental health can significantly improve overall employee resilience during change.
Measuring the Impact of Incremental Improvements
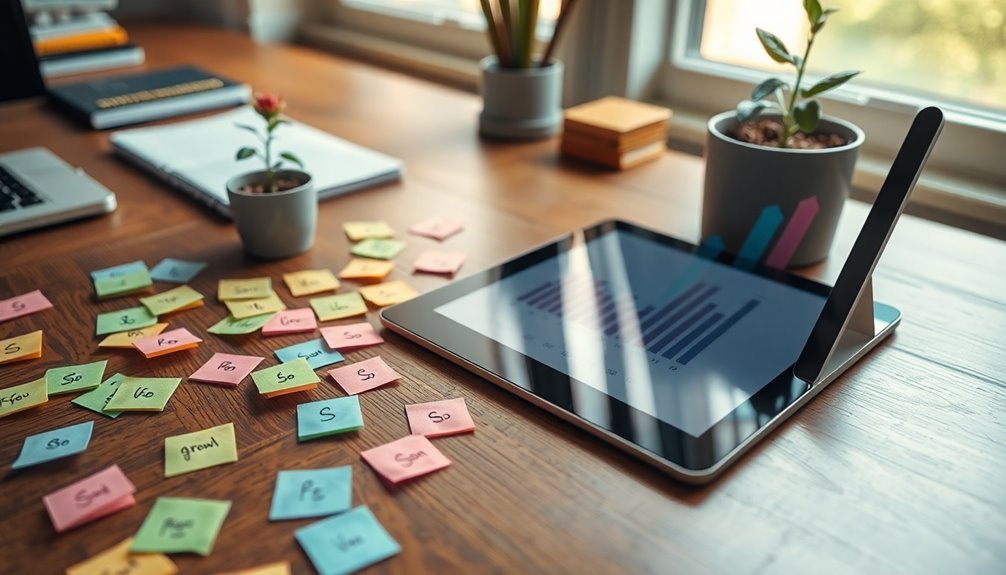
Measuring the impact of incremental improvements is essential for understanding how small changes contribute to overall performance. You should define clear metrics like cycle times, defect rates, lead times, and throughput, tailored to your specific process. Use tools to systematically observe and record data before and after each change, focusing on waste reduction and efficiency. Quantify gains through reductions in operator movement, space utilization, and resource consumption, which lead to financial savings. Establish baselines beforehand and schedule follow-up measurements at set intervals to track progress. Continuous data collection allows you to spot trends and detect process degradation. By measuring both quantitative and qualitative results—such as employee morale and customer satisfaction—you ensure your improvements deliver real, sustainable value. Incorporating insights from AI-driven data analysis can further enhance your ability to interpret results and refine your processes over time. Additionally, monitoring performance metrics helps maintain momentum and prevent regressions in process improvements. Engaging in dynamic communication exercises with your team can also foster a culture of continuous improvement and open feedback. Incorporating standardized measurement practices ensures consistency and accuracy in your data collection efforts.
Sustaining a Culture of Ongoing Progress
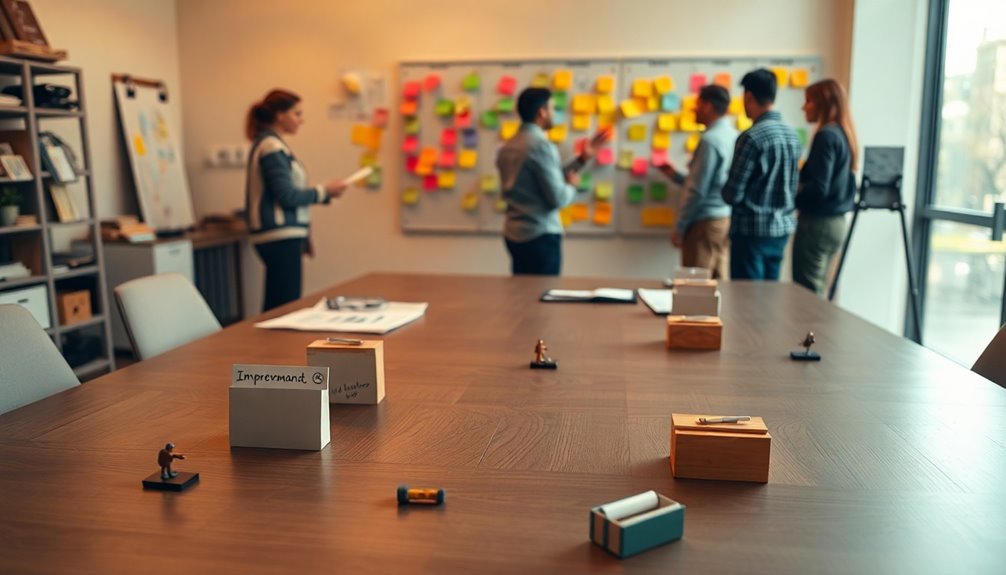
How can organizations guarantee that continuous improvement becomes ingrained in their daily operations? The key is leadership commitment. Leaders must clearly communicate goals, model desired behaviors, and reward efforts. Engaging employees at all levels fosters ownership, while providing training and establishing open channels for feedback keeps momentum alive. Developing structured programs like Kaizen, Lean, and Six Sigma ensures improvements are sustainable and standardized. To maintain progress, you should regularly monitor initiatives, adapt strategies based on feedback, and embed improvement practices into your culture. Strategic alignment ensures continuous improvement supports overall goals. By addressing resistance early, communicating benefits, and involving stakeholders, you create an environment where ongoing progress becomes a natural part of your organization’s DNA, not just a temporary initiative.
Frequently Asked Questions
How Can Small Improvements Lead to Significant Organizational Change?
You might wonder how small improvements can cause big change. When you make incremental adjustments, you reduce resistance and stay adaptable to shifting market conditions. Engaging employees in these small steps boosts morale and ownership. Over time, continuous refinement minimizes waste, improves quality, and streamlines processes. These tiny, consistent efforts build momentum, leading to sustainable growth and significant organizational transformation without overwhelming your team or disrupting operations.
What Role Does Leadership Play in Fostering a Kaizen Culture?
Your leadership role is essential in fostering a culture of continuous improvement. By showing unwavering commitment, communicating clearly, and leading by example, you build trust and motivate your team. Your active presence on the shop floor, coaching, and empowering employees encourage them to embrace small, incremental changes. Adopting an agile approach, you create an environment where experimentation and learning thrive, ultimately driving sustained organizational growth and innovation.
How Do Organizations Ensure Employee Participation in Continuous Improvement?
You can guarantee employee participation by creating a culture of trust and open communication, where ideas are valued. Encourage feedback through surveys, suggestion boxes, and brainstorming sessions. Provide training and resources to empower employees, and recognize their contributions regularly. Engage leadership to support initiatives actively, celebrate small wins, and track progress. When you foster an inclusive environment and show appreciation, you motivate employees to stay committed and contribute continuously.
What Tools Support Effective Problem Identification and Solution Testing?
You should use tools like the 5 Whys analysis and Fishbone Diagrams to identify root causes effectively. Pareto Analysis helps prioritize issues based on impact. Process Mapping and Flowcharts clarify workflows, revealing bottlenecks and redundancies. Control Charts and Performance Metrics Dashboards monitor process stability and performance, enabling you to test solutions quickly and see their effects in real time. These tools guarantee thorough problem identification and effective solution testing.
How Is Success Measured Beyond Cost Savings and Efficiency?
Imagine a clear river flowing steadily, showing more than just its speed. Success isn’t just about cost savings or efficiency; it’s about quality improvements, like fewer defects and happier customers. You also see progress in employee engagement, safety, and environmental impact. These signs reflect a thriving, resilient organization. You measure success by tracking customer satisfaction, process stability, safety records, and innovation, ensuring continuous growth beyond just numbers.
Conclusion
Embracing kaizen is like tending a garden—you plant small seeds daily, nurture them patiently, and watch as each tiny improvement blooms into lasting success. Remember, even a 1% daily progress adds up over time, transforming your workplace into a thriving, efficient space. Stay committed to continuous growth, and you’ll find that sustainable progress isn’t just a dream but a reality built one small step at a time.